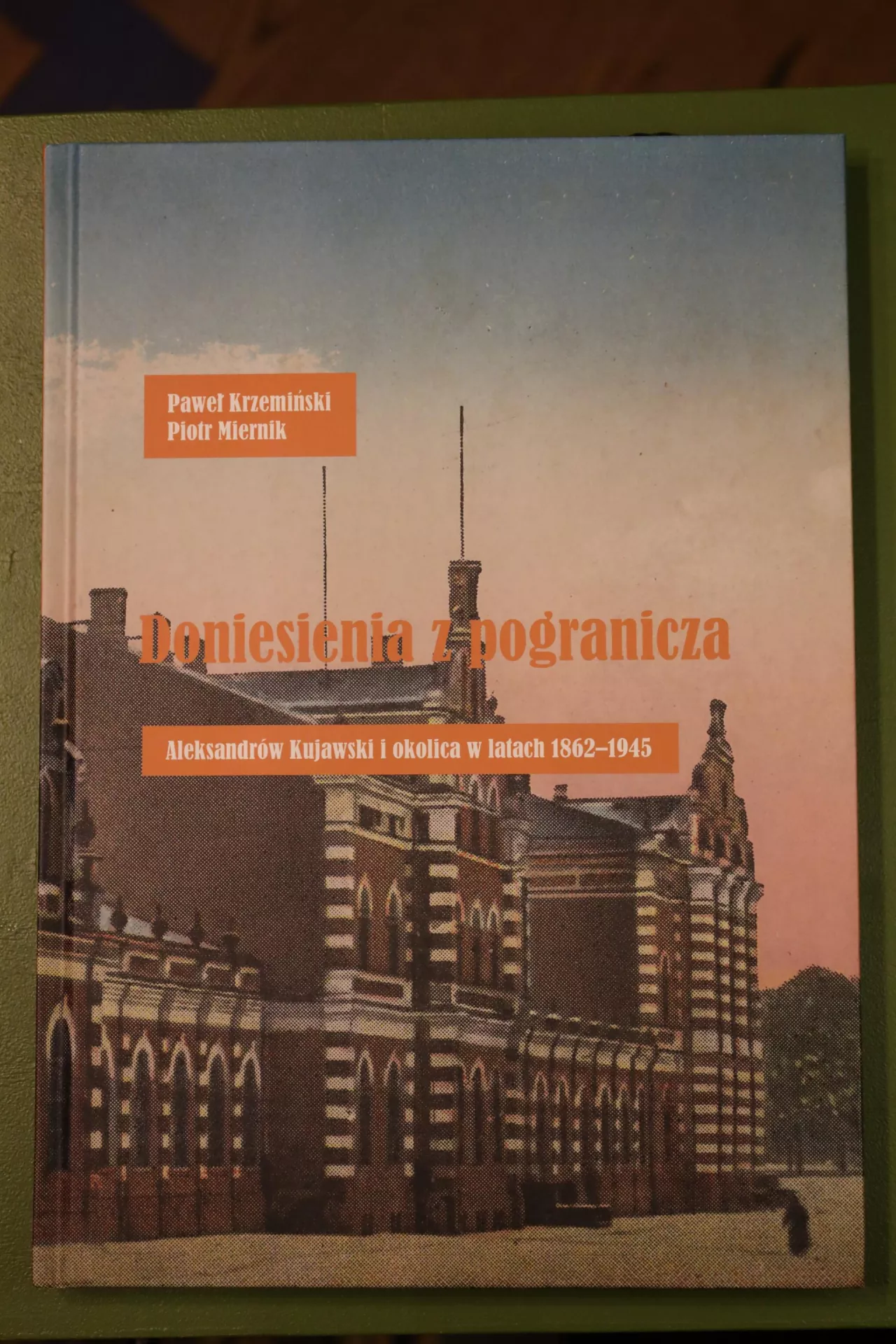
– W tym roku obserwujemy dosyć spore kolejki przy punktach skupu. Życzymy rolnikom, aby stali w jak najkrótszych, jednak dla nas to dobra wiadomość. Oznacza bowiem, że silosów BIN nie ma jeszcze w każdym gospodarstwie i że przed nami sporo pracy. Od ponad 20 lat robimy wszystko, aby zapewnić najlepsze warunki do magazynowania ziarna. Przed nami nadal wiele wyzwań – mówił rozpoczynając konferencję „6 mln ton ziarna w silosach BIN” Przemysław Bochat z działu marketingu kujawskiego producenta.
Firma BIN powstała
na początku lat 90. Początkowo najbardziej popularne były silosy liczące kilkadziesiąt ton pojemności. Dziś rolnicy zgłaszają przeciętne zapotrzebowanie na wielkości wynoszące kilkaset ton. Współcześnie firma słynie nie tylko z produkcji silosów z blachy ocynkowanej stawianych na płaskim podłożu i wyposażonych w perforowaną podłogę pozwalającą na działanie systemu aktywnej wentylacji. Od kilku lat wytwarzane są także silosy lejowe pod marką Konsil. Skierowane są dla przetwórców i rolników, u których dokonuje się szybka i częsta cyrkulacja ziarna. W ofercie są również silosy paszowe oraz szereg rozwiązań pozwalających na załadunek, wyładunek i transport ziarna. Odpowiadają za to podnośniki kubełkowe oraz przenośniki ślimakowe i redlery do ziarna.
– Mamy stosunkowo dużo planów. Myślimy nad nowymi wyzwaniami. Opracowujemy urządzenie do ekstrudowania przeznaczonego do produkcji pasz. Zamierzamy też wejść na rynek silosów o dużej pojemności. W tym celu przygotowujemy się do przeprowadzenia inwestycji, które pozwolą uruchomić technologię umożliwiającą nam zwiększenie pojemności naszych największych silosów do 4 a nawet 5 tys. ton – mówił Paweł Krzemiński, prezes zarządu firmy BIN.
Największy dotychczasowy silos BIN o pojemności 2200 to
Już w 2018 roku
BIN zamierza wytwarzać silosy wielkogabarytowe. Będą się one różnić od tych, które do tej pory można spotkać na polskiej wsi. Nie będą budowane z blachy płaskiej, lecz pofalowanej. Oznacza to wdrożenie zupełnie nowego procesu technologicznego. Niezbędne jest zbudowanie nowej hali produkcyjnej o powierzchni, co najmniej kilku tys. m2 oraz zakupienie nowych urządzeń i pras pozwalających na właściwe wyginanie, cięcie i falowanie metalowych arkuszy.
– Na duże silosy jest spore zapotrzebowanie. Nie tylko w kraju, ale i za granicą. Nie byliśmy w stanie produkować większych silosów, ponieważ nasza dotychczasowa technologia nie pozwalała na opracowywanie konstrukcji większych niż 2200 ton – mówił P. Krzemiński.
Konieczność pofalowania ścian dużych silosów spowodowana jest ograniczoną wytrzymałością ścian płaskich oraz grubością metalowych arkuszy, z których powstają. Mimo że falowanie powiększa ilość materiału potrzebnego na wycięcie ścian, faktycznie powoduje, że w procesie technologicznym koszty są ograniczane. Nie trzeba korzystać bowiem z drogich i grubych arkuszy stalowych.
– Zboże sypane do silosu, który ma ściany płaskie, zachowuje się jak woda. Prze w dół swym ciężarem na podłogę. Całe parcie słupa zboża skierowane jest na zewnątrz. Tak jak ciśnienie działa w każdym kierunku, tak słup zboża prze na boki. W związku z tym, cały ciężar ziarna w silosie przenosi się na ściany, które utrzymują lej. Potrzeba więcej materiału o większej grubości, aby konstrukcja wytrzymała to parcie. Osiągana jest wtedy większa wytrzymałość ścian bocznych na rozrywanie. Kiedy wprowadzamy blachę falistą wydaje się, że proces ten wymaga większej ilości blachy. Można jednak zastosować blachę cieńszą. Sfalowanie jest dodatkową składową i część tej siły, która normalnie parłaby w bok, kieruje w dół. Siła prze w układzie podłoże – ściana – tłumaczył Paweł Krzemiński.
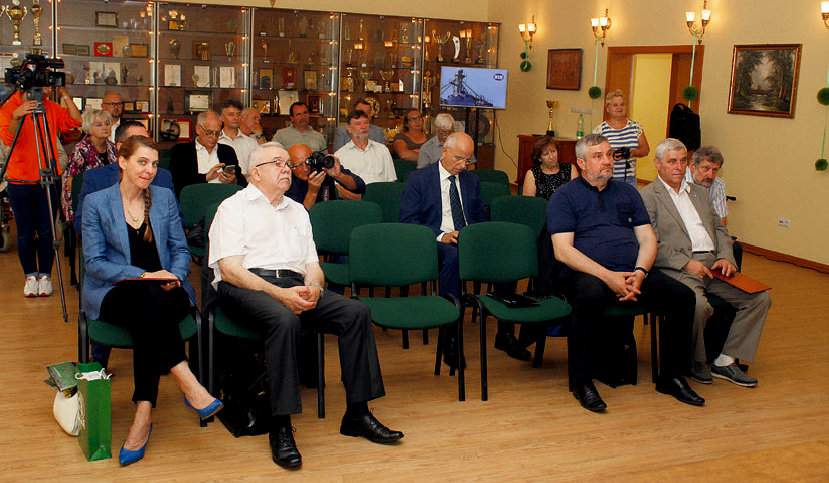
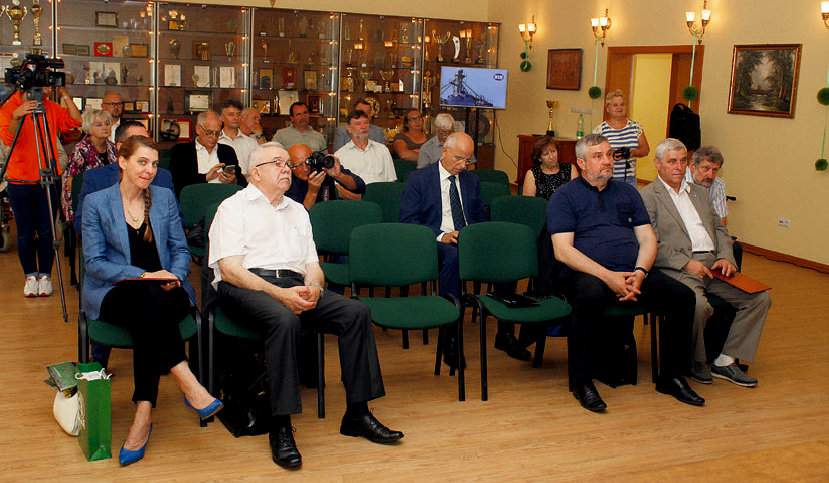
Skoro falowanie
powoduje, że można stosować blachę cieńszą, a więc tańszą, to dlaczego BIN nie stosuje tego procesu w dotychczas produkowanych silosach? Wszystko dlatego, że technologia taka wymaga dodatkowych wzmocnień konstrukcyjnych.
– Blacha przez swoją falistość jest harmonijkowo miażdżona, dlatego są stosowane podłużnice, które wzmacniają konstrukcję i zapobiegają zmiażdżeniu i spłaszczeniu blachy. W procesie produkcji zaś o wszystkim decyduje ekonomia. W małych silosach mniej blachy potrzeba na ściany płaskie. Gdybyśmy je zrobili z falistej i dołożyli podłużnice zewnętrzne, tej blachy byłoby więcej. Natomiast przy większych i wyższych silosach proporcje się odwracają – wyjaśniał prezes BIN.
Od wielu lat silosy są budowane z bardzo dobrej jakościowo blachy sprowadzanej z Finlandii od firmy Rautaruukki. Od 2014 r. została ona częścią szwedzkiego koncernu SSAB, a jej nazwa została zmieniona na Ruukki Construction. Zmiana właścicielska nic w procesie produkcyjnym BIN nie zmieniła i stalowe arkusze do produkcji silosów nadal są z fińskiej huty sprowadzane.
– Często dostaję propozycje poszukiwania blachy na Ukrainie. Ma być tam tańsza. Jak do tej pory, nie złamaliśmy się i nie używamy tańszej blachy. Stawiamy na jakość. W procesie produkcyjnym korzystamy nie tylko z blachy o grubości 1 i 1,5 mm. To zależy od pojemności silosu. Stosujemy także 2,5 i 3 mm. Gdybyśmy chcieli zrobić silos o pojemności 4,5 tys. ton, to musielibyśmy zastosować blachę 6 – 8 mm. Tylko że taka po prostu nie jest produkowana. To dlatego zdecydowaliśmy się na opracowanie procesu falowania – opowiadał Paweł Krzemiński.
BIN od lat słynie
z produkcji silosów płaskodennych. Gwarantują one odpowiednie warunki przechowywania zboża przez długi czas. Wszystko przez zastosowanie płaskiej perforowanej podłogi. Kiedy w procesie aktywnej wentylacji wtłaczane jest przez nią powietrze, jest ono rozprowadzane równomiernie na całej wysokości ziarnowego słupa, przez co dochodzi do skutecznego wentylowania. Dzięki temu ziarno nie traci swoich parametrów. Początkowo poważną wadą silosów płaskich była niedoskonałość sytemu wyładowczego. Pierwsze wersje miały rękaw, który wybierał ziarno ze środka. Powstawał jednak odwrócony w środku stożek zboża i w zależności od pojemności wiązało się to z koniecznością ręcznego wygarnięcia ziarna. Obecnie silosy BIN mają wewnętrzny ślimak, który pracuje na podłodze jak wskazówka zegara. Przenośnik pracuje po obwodzie i odpycha ziarno od ścian do środka. W ten sposób zboże wyciągane jest na zewnątrz. Jednak i to rozwiązanie nie jest idealne, ponieważ zawsze kilka kilogramów resztek ziarna pozostaje w środku. Są one znikome, jednak oczekiwania rolników są różne. Niektórzy nie chcą z różnych względów wchodzić do środka, dlatego wybierają droższe konstrukcje lejowe.
– Silosy lejowe mają zasadnicze wady. Są średnio dwa razy droższe od płaskodennych i przechowywanie w nich zboża nie może być długoterminowe. Świetnie jednak sprawdzają się wszędzie tam, gdzie wielokrotnie w ciągu roku opróżnia się silos. W punktach skupu, w firmach nasiennych, na fermach przy produkcji zwierzęcej, duży obrót zboża powoduje, że opłaca się silosy lejowe stosować. Przechowywanie w nich zboża nie jest tak długotrwałe. Natomiast w innych przypadkach przy konieczności efektywnego napowietrzenia i wentylacji ziarna silosy płaskodenne BIN są bezkonkurencyjne. W tym roku planujemy zwiększenie pojemności produkowanych silosów lejowych aż do 300 ton – zapowiedział Wojciech Kaszubski, właściciel firmy Konsil, która odpowiada za sprzedaż silosów lejowych produkowanych w Aleksandrowie Kujawskim.
Tomasz Ślęzak